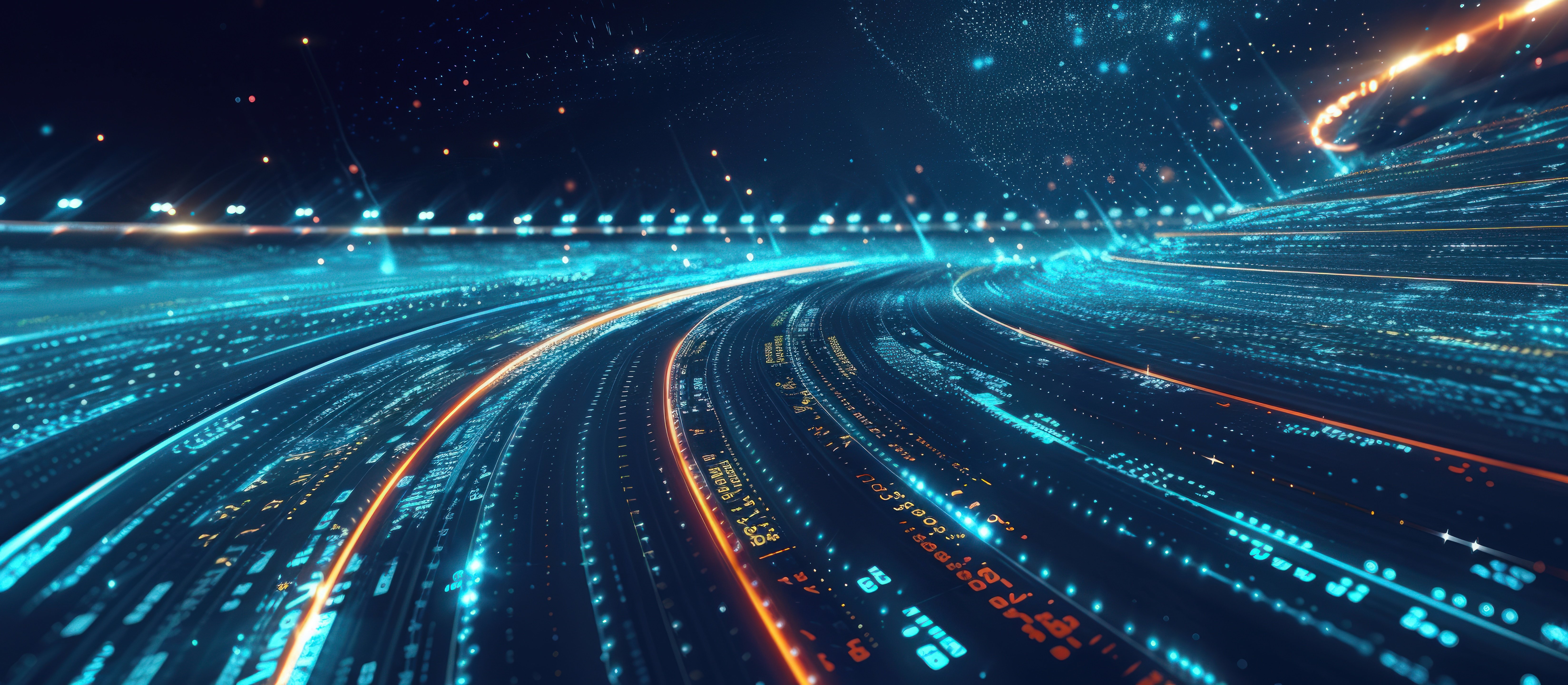
Meet the Team: Viral Vector Development & Manufacturing
Meet Kyle Anderson, Ph.D., Director of Manufacturing Science and Technology (MSAT) at Resilience RTP, North Carolina & Xiaotong Fu, Ph.D., Head of Downstream Process Development and Pilot Operations at Resilience Boston, Massachusetts. These two leads from our Gene Therapy team collaborate extensively to bring client's viral vector programs to life. We recently sat down with them to learn more about their collaboration strategies, how they are solving viral vector development & manufacturing challenges, and what drives them to continue their work in cell and gene therapy.
WHAT YOU WILL LEARN IN THIS VIDEO
- - Discover how the Process & Analytical Development (PAD) team and GMP manufacturing team collaborate to offer best-in-class services for viral vector (AAV, LVV) development and manufacturing
- - Hear how their approach allows them to deliver a GMP batch of viral vector in under 12 months
- - Uncover which challenges the teams are solving for and how they are rising up to meet the industry demands for viral vector products
Below is a transcript of the conversation, edited for clarity. Interested in meeting with our team to discuss how we can support your viral vector needs? Connect with us today!
Q1: What motivates you to work in viral vector development and manufacturing?
KYLE
For me, it's the fact that we are manufacturing cures. It's very rewarding to manufacture treatments, but here at Resilience, we get the chance to manufacture cures for patients. It's super inspiring.
XIAOTONG
I joined the gene therapy field because it is an emerging modality targeting underserved patient populations. Most of the gene therapy companies were targeting ultra-rare diseases which could be the only hope those patients have. Gene therapy is full of technical challenges and unknowns, so it is very exciting to me that I can use my skill set and knowledge to navigate through an unknown territory with the possibility of bringing hope to the patient and joy to their families. That's the most rewarding part of my career and that's what motivates me to work in this field.
Q2: Can you tell us about the tech transfer infrastructure that your team has built to ensure you can deliver a GMP batch of viral vector in under 12 months?
KYLE
I've worked in manufacturing sciences for my entire career and in all that time, I've had wonderful relationships with my colleagues in process and analytical development (PAD). But here at Resilience, it's at a whole other level. We have an incredibly tight collaboration with our development colleagues. We talk with them all the time and frequently share technical expertise. One of the great things about the platforms we run is that there is so much overlap between what the process development lab can do and what we can do here at the GMP facility. We use the same equipment, methods, and documentation, with minor modifications. We try very hard to be extremely efficient in how we work with our PAD colleagues. One of my favorite aspects of that relationship is when our development team is executing, for example, a pilot run or a small scale run, we'll send people up to the development lab to observe.
Most of the time, we're talking about people from RTP putting on gloves, putting on a lab coat, getting in the development lab and helping the development team execute the development scale batches.
In that way, being able to directly apply the learnings done in the development lab to what we do here at the GMP facility in RTP is very effective and allows us to be efficient. And we don't restrict that opportunity to people on the tech transfer team. We send anybody who would benefit from hands-on interaction with the process in the lab environment, there's an opportunity to go up and build relationships and, again, be very, very efficient and make sure that we have as much process knowledge here in RTP as possible. And in that way, we can deliver products in very, very fast.
XIAOTONG
I can break this question into two parts. First, at Resilience we take a modular approach to vector manufacturing instead of creating platform processes from end to end. The beauty of this approach is that each unit operation or particular assay can be treated as an individual module. So, our teams just need to focus on building capabilities around these modules instead of creating something end-to-end. Of course, every molecule, every program, has different tech transfer needs. So all we need to do when a new molecule comes into tech transfer is assemble the right building blocks with minimum tweaking, and put them together. that'll be our process instead of doing tech transfers from the ground up every single time.That's where we gain a lot of speed and efficiency.
Secondly, I can't emphasize how much our manufacturing team and process development teams interact. We actually start the conversation around tech transfer at the beginning of the process and analytical development work. What that means is that both teams are already aligned on the process and assays even before we officially start tech transfer. We share a lot of synergies in terms of equipment capabilities, best operation practices, even training! We give each other plenty of opportunities to ask questions, learn from each other, and address any facility gaps, feedback gaps, or concerns.
Q4: What challenges is Resilience solving in viral vector manufacturing?
KYLE
We're working very hard to have unique offerings that can ensure we can get high-quality viral vector batches out to patients as quickly and efficiently as possible. Our new SnapLVV and our Essential AAV & LVV offerings are great opportunities for clients who have a great idea to get it into a GMP manufacturing facility and turn that idea into an actual product that is administered to actual patients. There are many researchers out there with really great ideas and being able to turn those ideas into products is hard, it takes a long time and is very expensive. With these new offerings, we aim to provide a fast and efficient way for innovators to turn their ideas into an actual product.
One of the things that I always make sure to tell my kids is that practice really does make perfect. And here in RTP, along with our colleagues up in development, we practice these platforms a lot. We have a lot of experience in the unit operations that are necessary to manufacture any of these programs. That experience, even if it's generated with a different product or one vector, is relevant for other products and other vectors. And so we practice these platforms over and over and over again. By getting clients to use SnapLVV or Essential, we're able to get new products very quickly into our platforms because of that practice and that extensive experience. And then from that development lab scale very quickly into the GMP facility.
XIAOTONG
We're trying to offer a way for viral vector manufacturing to be done cheaper and faster, while meeting all of the stage-appropriate CMC requirements. We leverage a modular approach to do that and build flexibility with this method.
This industry moves fast, and if in a couple of years down the road, the company strategy starts to pivot, we should be able to quickly adapt to it and provide alternatives. Since Resilience has a large network with integrated capabilities, we are able to do that.
Q5: Which Resilience Phenotype best describes you?
The phenotype that best describes me is ownership. My team & I feel a very strong sense of ownership for the processes that we bring in and the products that we make. We strongly feel that the success of the client is our success. When we're looking at a problem, we feel ownership to solve it with the client. We want to make sure that we're not just doing things the same way they've always been done or the same way our previous companies did them. We want to think outside the box and come up with creative ways to get these products out to patients in need. I love the fact that I work with 150 other people here at RTP and beyond, especially with my colleagues in the development space, who feel the same way.
XIAOTONG
The phenotypes that best describe me are builder mentality and grit. As I mentioned, gene therapy is full of technical challenges and unknowns, even nowadays. Building something from scratch requires you to have a specific mentality. It's not just about having the knowledge and skills, you also need creativity, to be brave with uncertainties, navigate through unknowns, and be ready for new challenges. I think that mindset combined with the desire to build something from the ground up and keep pushing the boundary, are very important in order to thrive in the gene therapy field.
Have a question for our team? Connect with us today!